The best technology, materials and our
know-how: RELINE has been constantly advancing the production processes of GRP technology since 2009.
Glass fiber reinforced plastic (GRP) is one of the most versatile materials that can be designed and used successfully in numerous industries such as the aircraft, automotive, shipbuilding or wind turbine industries.
As a high-quality fibre-reinforced composite (FRP), GRP is produced by combining several materials - the moulding matrix such as polyester, vinylester or epoxy resin and reinforced high-strength fibres (usually glass, aramid or carbon).
With GRP technology, RELINE offers an optimal GRP pipe liner for trenchless pipeline rehabilitation that is tailored to the static requirements of the sewer, the quality of the wastewater or other media and the given safety requirements.
Materials of the highest quality - special ECR glass fibrer and a resin adapted to UV light curing - form the basis for this successful GRP technology. This enables optimal curing with innovative UV light curing and long-lasting quality of the end product.
GRP TECHNOLOGY
INNOVATIVE TECHNOLOGY
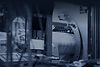
Economical and safe: The Alphaliner with integrated sliding protection and integrated preliner
All Alphaliners are equipped with integrated sliding protection or optionally with an integrated preliner. This increases the speed of construction and safety during installation. Depending on its size and weight, the pipe liner material is exposed to considerable frictional forces during installation . Even small irregularities or sharp-edged obstacles, which may still be present despite careful preparation of the channel with milling robots, are capable of damaging the outer casing and thus impairing the functionality of the pipe liner.
The Alphaliner with integrated preliner also offers additional protection against contact of the pipe liner with water. This all-round protection prevents the resin from coming into contact with water in the event of damage to the outer skin. In addition, the Alphaliner is equipped with integrated sliding protection in the lower area with an additional stable outer skin that is firmly welded to the tubular liner. In the variant with integrated preliner, the tubular liner is supplied complete with an additional outer cover.
Defined wear layer ensures long service life
The Alphaliner has a unique protective wearing layer, which is defined in terms of its thickness, on the interior surface of the liner, thereby complying with the requirements of DWA-A 143-3 and DIN EN ISO 11296-4. The Alphaliner's protective wearing layer does not count as part of the composite wall thickness (the part of the composite liner wall which is structurally relevant). The Alphaliner500G is made of a particularly stable, resin-saturated glass nonwoven with a thickness of at least 0.3 mm. The Alphaliner1800H consists of a resin-saturated high-quality polyester fleece with a thickness of minimum 0.5 mm.
This protective wearing layer is at least twice as thick as the abrasion resistance established by the Darmstadt Tipping Trough Trial and protects the Alphaliner against mechanical wear and stress, e.g. during high-pressure flushing. The Alphaliner has a lot of very high safety reserves ensuring a long service life of typically at least 50 years and more.
Clean, safe, fast - the installation of the Alphaliner
Installation and curing of the Alphaliner are characterized by uncomplicated handling and fast processing of the entire construction project. Up to several 100 meters of sewer pipe can be renovated in one working day. The pipe is once again in service in hardly no time at all. Traffic congestion, noise and dust pollution caused by the job site are all significantly reduced.
-
Preparation by means of HP cleaning and any grinding work
-
Camera inspection to assess the condition of the sewer
-
Drag-in the Alphaliner with a cable winch and, if necessary, with the help of a conveyor belt
-
Curing the Alphaliner using UV light source and special UV lamps
-
Checking and documentation (online) of the curing process based on measured curing parameters
-
Leak test and taking a linersample for quality control
-
Re-opening of laterals using a milling robot
-
oper sealing of the liner to the manhole and leak tight re-connection of the Alphaliner to the side inlets
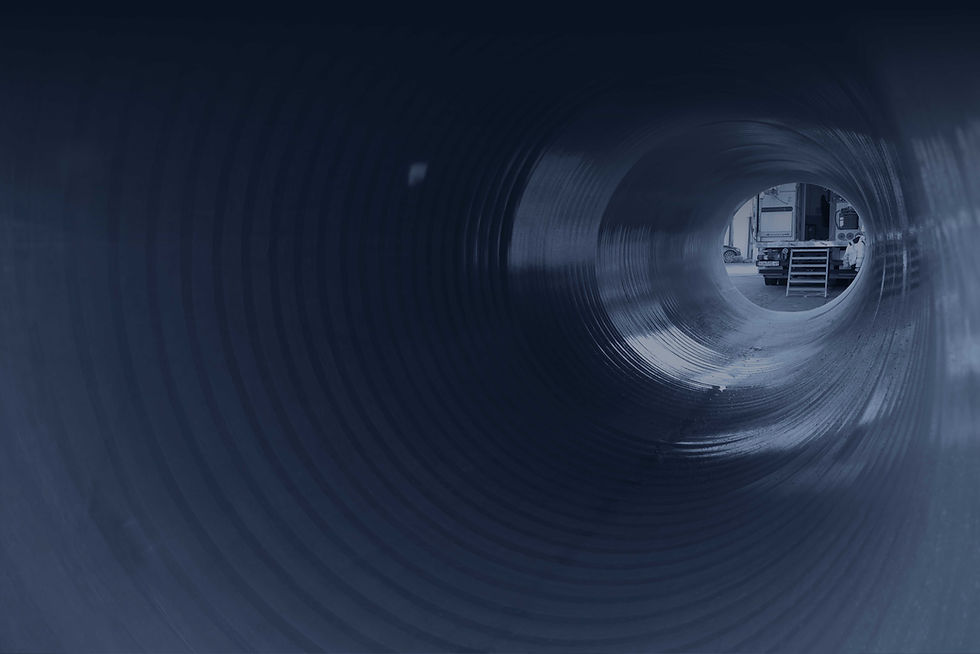
Glass fiber reinforced plastic (GRP) is one of the most versatile materials that can be designed and used successfully in numerous industries such as the aircraft, automotive, shipbuilding or wind turbine industries.
As a high-quality fibre-reinforced composite (FRP), GRP is produced by combining several materials - the moulding matrix such as polyester, vinylester or epoxy resin and reinforced high-strength fibres (usually glass, aramid or carbon).
With GRP technology, RELINE offers an optimal GRP pipe liner for trenchless pipeline rehabilitation that is tailored to the static requirements of the sewer, the quality of the wastewater or other media and the given safety requirements.
Materials of the highest quality - special ECR glass fibrer and a resin adapted to UV light curing - form the basis for this successful GRP technology. This enables optimal curing with innovative UV light curing and long-lasting quality of the end product.
INNOVATIVE TECHNOLOGY
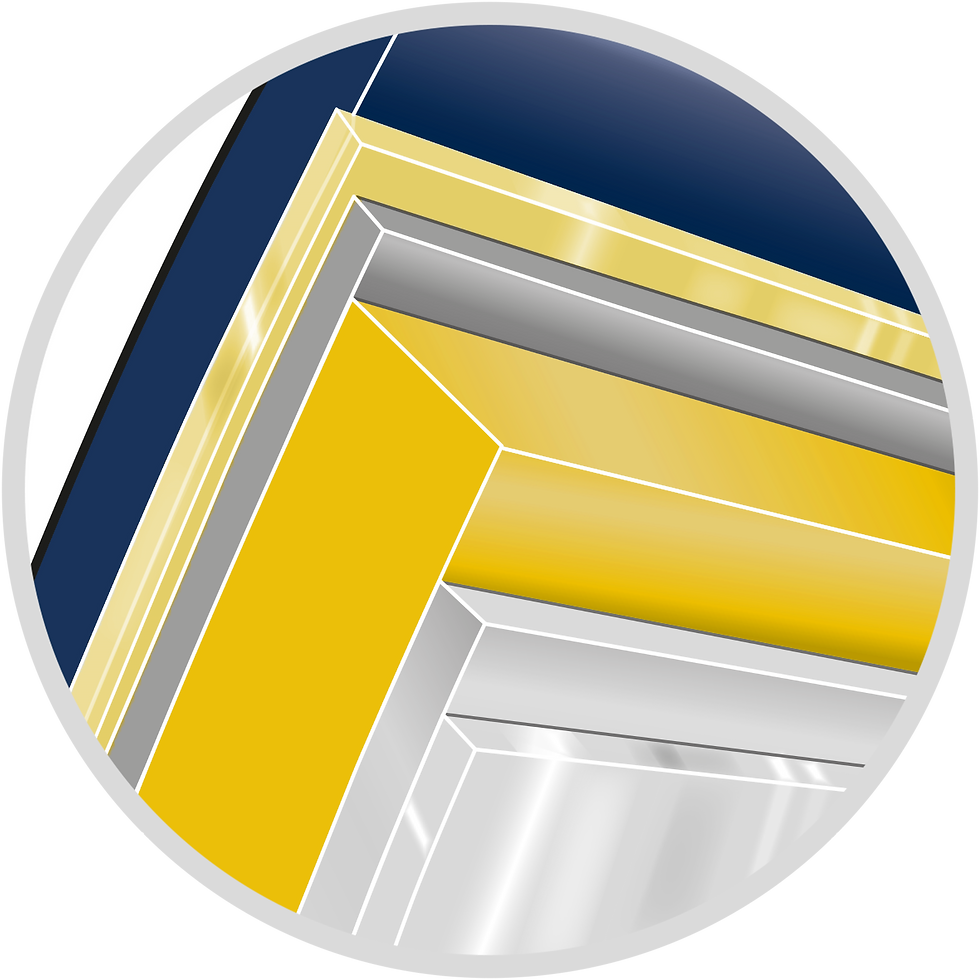
WELL-PROVEN DESIGN
The innovative design of the Alphaliner stands for endless areas of application and stands out with properties that set high standards:
-
UV light-proof, fabric-reinforced PVC outer protection, optionally as integrated sliding protection or integrated preliner.
-
Polymer film (PA) with styrene barrier function.
-
Load-bearing thickness of the composite structure consisting of ECR glass fibres for Alphaliner500G or for Alphaliner1800H. Formed out of wrapped pre-impregnated glass fibre layers.
-
Abrasion protective layer against highest chemical and mechanical loads.
-
Inner foil (PE/PA) as installation aid with styrene barrier (generally removed once curing is completed)

Glass fiber reinforced plastic (GRP) is one of the most versatile materials that can be designed and used successfully in numerous industries such as the aircraft, automotive, shipbuilding or wind turbine industries.
As a high-quality fibre-reinforced composite (FRP), GRP is produced by combining several materials - the moulding matrix such as polyester, vinylester or epoxy resin and reinforced high-strength fibres (usually glass, aramid or carbon).
With GRP technology, RELINE offers an optimal GRP pipe liner for trenchless pipeline rehabilitation that is tailored to the static requirements of the sewer, the quality of the wastewater or other media and the given safety requirements.
Materials of the highest quality - special ECR glass fibrer and a resin adapted to UV light curing - form the basis for this successful GRP technology. This enables optimal curing with innovative UV light curing and long-lasting quality of the end product.
INNOVATIVE TECHNOLOGY